DTManager
The software to coordinate the various components of an automated production line and track the relative information
The story of DTManager began in the metal heat treatment sector. It was first marketed as a supervision system for controlling furnaces, then developed to manage production lines with complex architecture.
The aim is to coordinate all components, optimising the production process and guaranteeing what has always been its distinguishing features: efficiency, operational completeness and ease of use for operators.
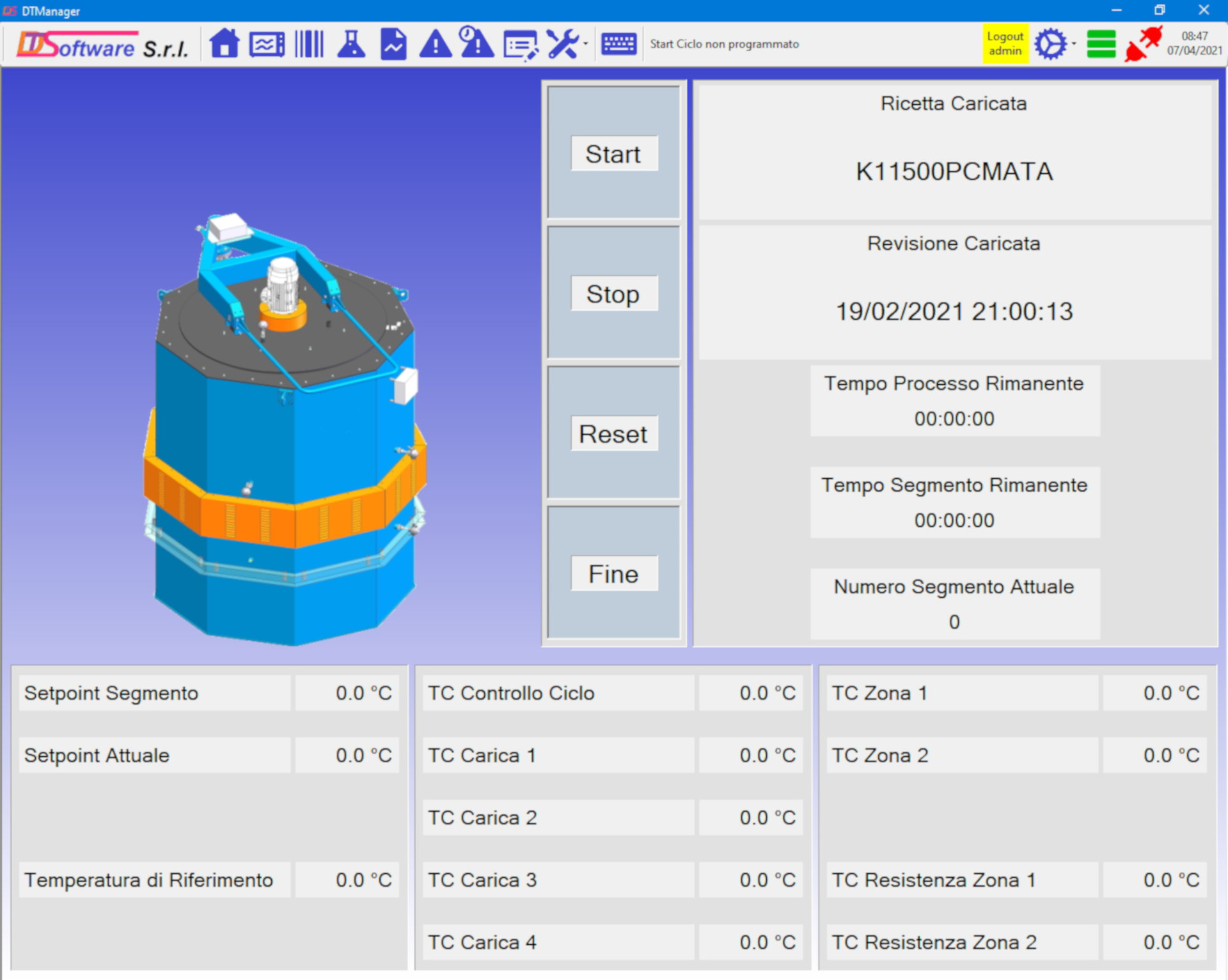
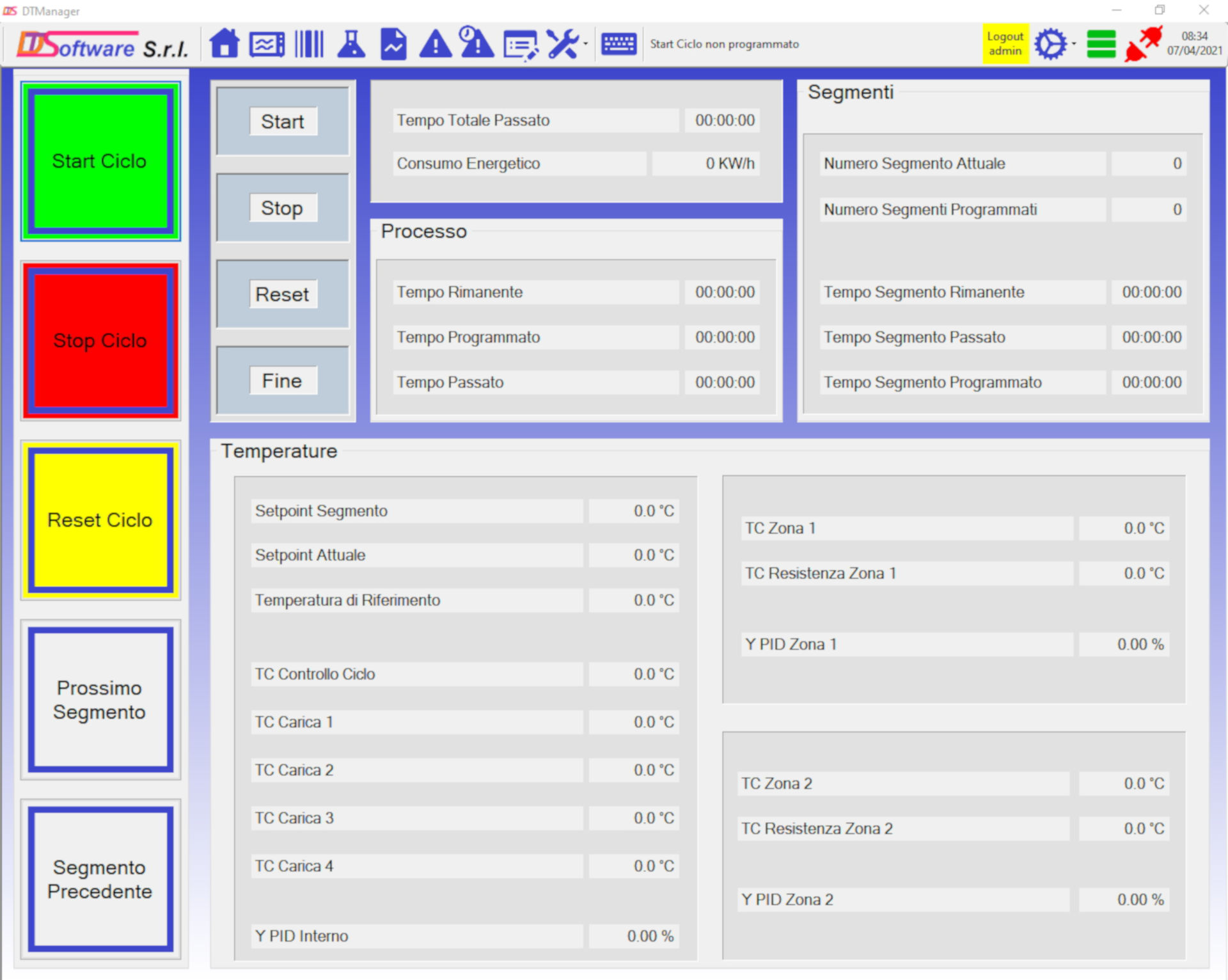
- operational: controls, instrument settings and real-time display of system status;
- diagnostic: alarm logs, warnings, messages and user operation tracking;
- coordination: organisation and optimisation of the production process;
- management: creation and recall of recipes, real time modification of setpoints;
- data recording: collection of information for complete process traceability;
- access to collected data: real time customisable graphs;
- reporting: creation of production and diagnostic documentation.
DTManager consists of modular functional blocks in a perfectly integrated architecture to meet even the most complex expectations.
The software is available in various packages, each with a different set of functions, allowing customers to find the right solution tailored to their specific needs.
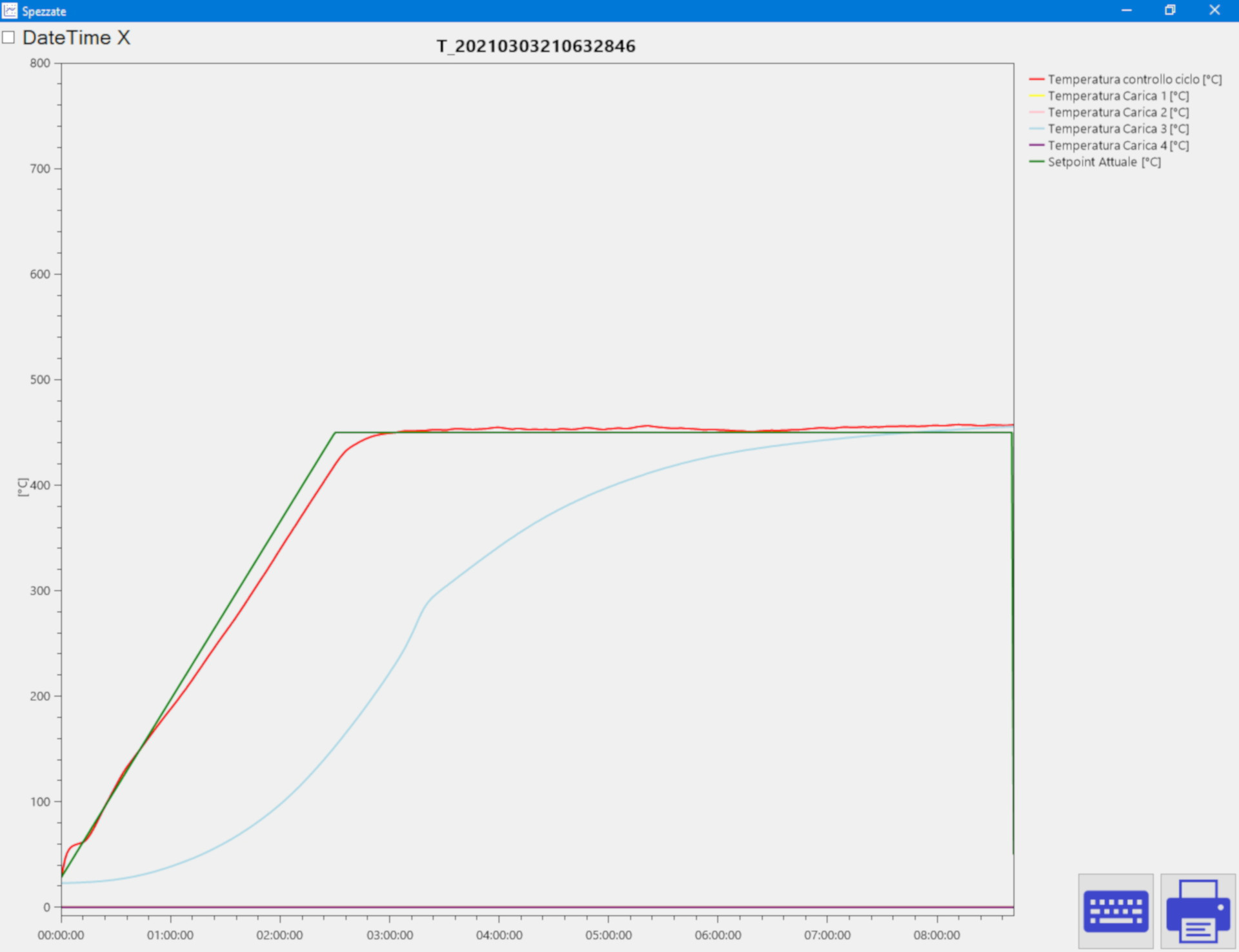
Choose the package that suits you best
Device
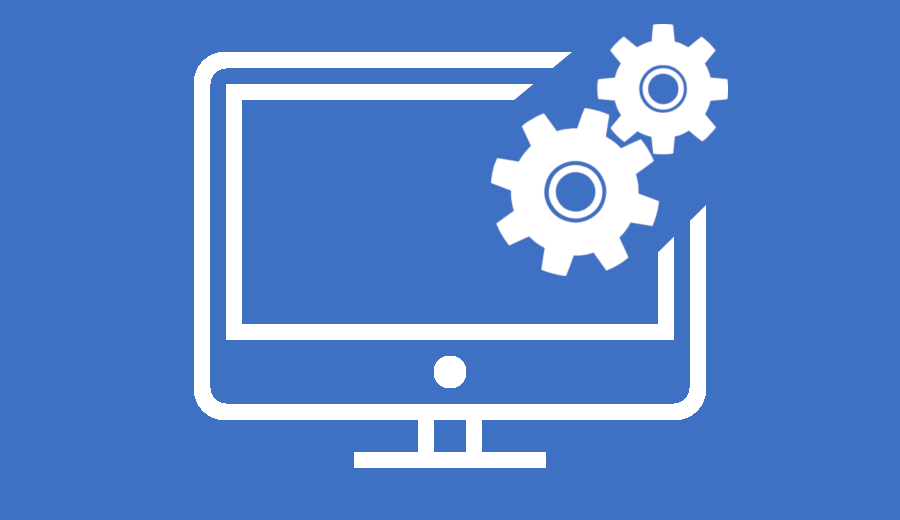
An industrial PC with its own graphic interface dedicated to hosting both the SQL server and supervision system. A lean, compact, functional solution to manage even a highly complex single automation and keep data records for a defined period of time.
Core
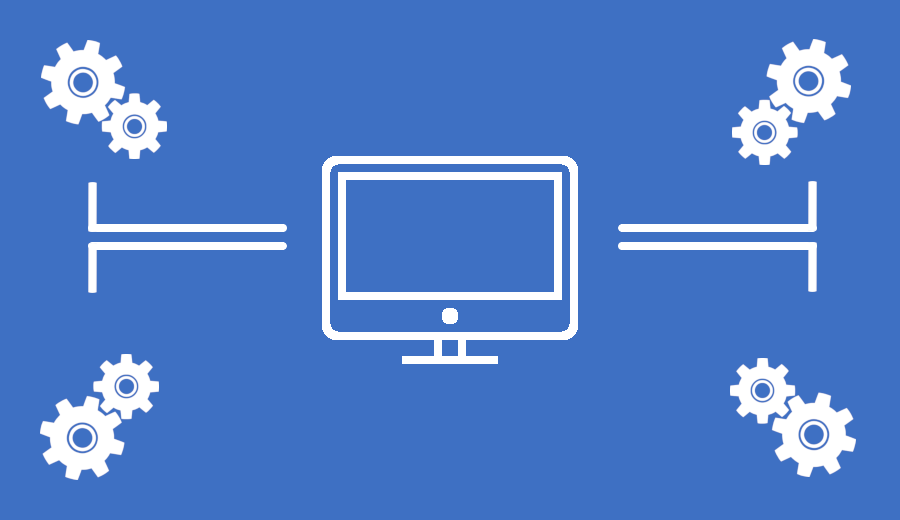
The supervision software and SQL server can be hosted on a dedicated PC or on a machine already present in the company network. The system can manage a number of automations at the same time, with an exchange of data between the various client stations, controlling a multi-stage production process.
System
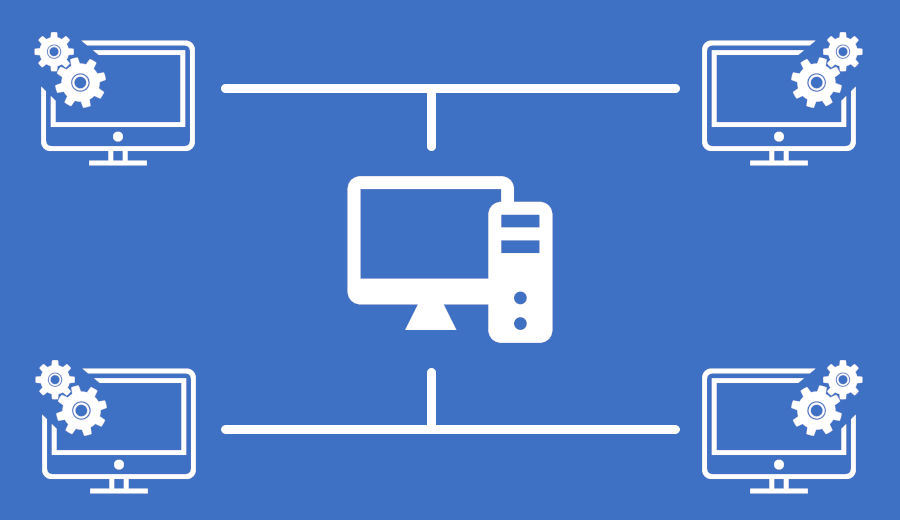
The core and device combination. A centralised system is combined with several local systems to ensure full and functional operation and tracking of each constituent element of the production line, even in the event of disconnection from the central server, thanks to automatic restoration of locally recorded data in a situation of isolation.
Our experience at the service of customers

Process optimisation
Improving the performance of existing equipment.

HW and SW upgrade
Effectively targeting lengthy equipment modernisation processes.

Remote start-up
Start-up of an entire production line remotely in full lockdown.

Rapid intervention
Swift problem solving is what makes the difference.

Electronics repairs
Solving electronics problems on obsolete equipment.
DT Software can improve the performance of your company NOW!
Contact us